Four Ways Flexible Packaging Can Strengthen a Circular Economy
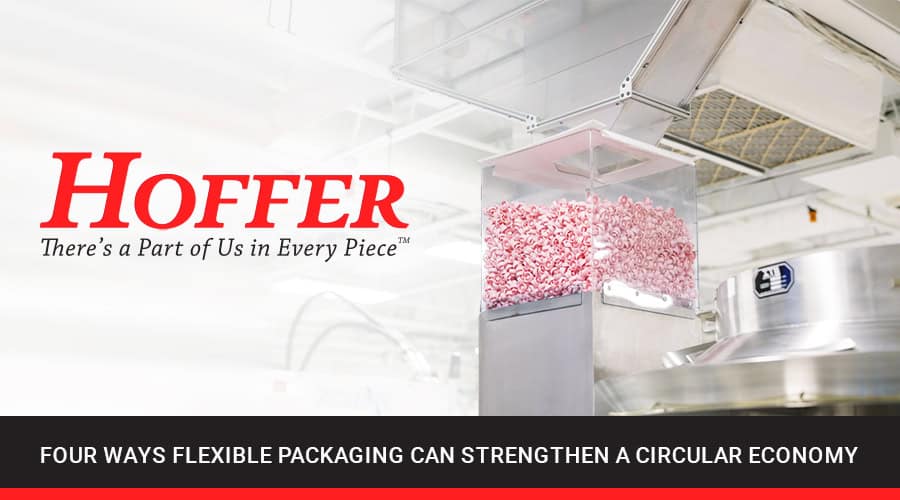
Sustainability can’t be something we just talk about in the plastics industry. Not when 87% of the public is worried about the impact of plastics on the environment, according to Accenture.
That’s why companies across the country are working to transform the traditional model of plastics production, use and disposal. Circularity ensures that every stage of a product’s life – from design to disposal – is planned to maximize resource efficiency and minimize waste. Instead of the old linear approach, the developing circular economy aims to reduce, reuse and recycle our resources in a continuous loop to keep materials and products in circulation for as long as possible.
Legislation in several states is elevating the urgency of these efforts. Illinois, home to Hoffer Plastics, is among those exploring a concept called extended producer responsibility (EPR). It would require brands to help build and manage the recycling systems for their products.
So, how does the increasing popularity of flexible pouches fit in? Let’s look at four ways flexible packaging can become part of a circular economy.
1) Material Innovation
Components of traditional flexible pouches often must be separated at time of disposal. Today, there are an increasing number of mono-material solutions that make recycling a lot easier for consumers – with the right infrastructure. From the film to the cap and spout, these solutions can be recycled as one unit to avoid landfills and remain part of a circular economy.
Caps and spouts are often made using polyethylene (PE) and polypropylene (PP). These are proven performers in numerous flexible packaging applications. Plus, we’ve been able to work with suppliers and customers to use resins with as much as 30% post-consumer recycled (PCR) material in the caps and spouts that we mold for flexible packaging.
2) Design Optimization
Flexible packaging is perfect for today’s convenient grab-and-go applications. But in traditional designs and formats, these applications can create complexity when moving toward a circular economy.
For a quality product that pleases consumers, the spout and cap can’t just be recyclable. They must deliver on key performance parameters including:
- Tamper-evident design
- A tight seal
- Choke proofing and other safety considerations
- Aesthetics
- Ease of use
Getting all that right – while implementing compatible, recyclable materials and reducing overall material use – is no small challenge. But it’s one we continue to focus on at Hoffer Plastics. And we’ve made great progress on lightweighting designs of our fitments to use less plastic while maintaining performance. Not only does this make recyclability easier for many, it reduces the amount of raw materials and energy required to manufacture caps and spouts.
Case in point is our P-15 Trust-T-Lok™ cap – which we redesigned with 46% less material. Here’s more about Trust-T-Lok flexible packaging caps and closures.
3) Supply Chain Collaboration
At first glance, flexible packaging appears to offer some advantages for a circular economy. It uses less material than other rigid packaging options. It’s also lighter and more compact – reducing the carbon footprint of shipping and storage.
However, creating a true circular solution will take everyone involved in the life of a product’s packaging, including:
- Brands
- Machine manufacturers
- Resin suppliers
- Film extruders/converters
- Caps and spouts suppliers, like Hoffer Plastics
- Contract manufacturers (co-manufacturers and co-packagers)
- Distributors
- Retailers
- Recovery and recycling facilities
- Consumers
For example, do you want a pouch, cap and spout all made of polyethylene (PE) – including PCR materials? Great! That’ll make it truly “circular.” But PE has a low melting point. And it can’t handle a lot of heat for proper sealing. So, your material supplier, machine manufacturer, cap and spout supplier, and contract manufacturer will need to collaborate to deliver a recycle-ready, high-quality and safe solution.
4) Supply Chain Sustainability
Long before packaging reaches consumers, every company in the packaging supply chain has opportunities to be a responsible, sustainable partner – beyond recyclable products.
For example, at Hoffer, we save and regrind much of the waste plastic in our injection molding processes. As a result, we’re able to divert 300,000 pounds of material from landfills each year.
With the commitment of every member of your supply chain – from your co-manufacturer to your packaging machine supplier to your cap and spout manufacturer – you can establish a team committed to minimizing its overall environmental footprint from start to finish.
Let’s Achieve Flexible Packaging Circularity Together
We’re excited about the potential of flexible packaging in a circular economy. But teamwork is crucial to realize the vision for a more sustainable future.
Together, we can drive greater sustainability, efficiency, safety and consumer satisfaction. Contact us today to explore how we can help with your flexible packaging program!