Small Parts, Big Impact: Micromolding Fuels the Next Generation of Medical Devices
Every player in the medical device manufacturing industry is always on the lookout for the next big breakthrough. But what about the small ones – literally? As medical technology advances, components continue to shrink, requiring tighter tolerances and faster production speeds. While these challenges may seem complex, one manufacturing process continues to fuel innovation: micromolding.
Micromolding is rapidly becoming the backbone of medical device manufacturing, allowing the creation of miniature parts that adhere to strict quality standards. Successful integration of micromolding into the medical device manufacturing process require expertise across the full development cycle – from prototyping and design for manufacturing (DFM) to precision tooling and scaling efficiently to production.
Accelerating Medical Device Innovation with Micromolding
A growing trend in micromolding is its use in low-volume prototyping to save time and cost while identifying potential issues prior to the transition to production.
Traditionally, companies may leverage additive manufacturing practices like 3D printing to design prototypes. While these methods can be useful for early-stage concept validation, it lacks the insights into material properties and precision required for full production.
Micromolding enables engineers to rapidly produce precise, functional prototypes for evaluation before transitioning to full-scale production. This process enables manufacturers to test designs, assess material compatibility and refine complex features. Micromolded prototypes allow engineers to simulate real-world performance, ensuring validation of functionality, tolerance checks and that the final product meets both performance expectations and strict regulatory requirements. This early-stage low-volume prototyping is critical for identifying potential design or performance issues, making necessary adjustments and avoiding costly delays in later stages of production.
This ability to rapidly iterate and test is particularly vital for medical devices like wearables and non-invasive components. For instance, in devices such as diagnostic tools and sensors, micromolding not only facilitates the creation of lightweight and compact components but also ensures they are durable and capable of withstanding prolonged use, crucial for patient safety and device reliability.
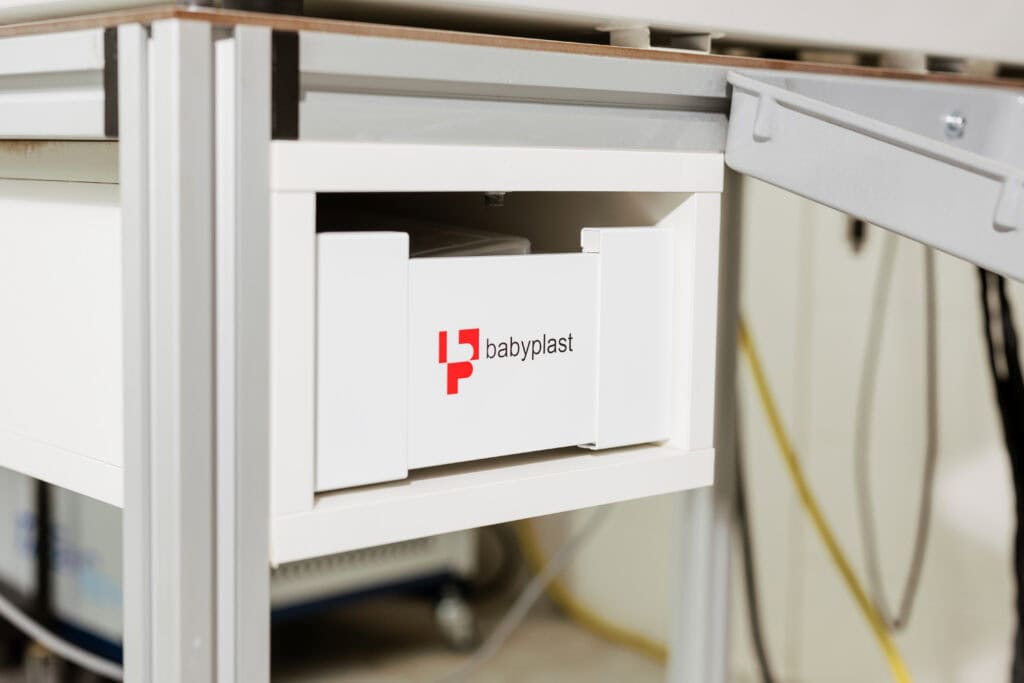
While micromolding is becoming more accessible as a prototyping tool, developing a successful prototype is just the first step. Uncover three key areas of expertise that drive quality, efficiency and production readiness in your micromolded parts.
1. Design for Manufacturability (DFM)
Prototyping is a critical component of Design for Manufacturability (DFM) – but it’s only part of the process. In micromolding, Design for Manufacturability (DFM) plays a crucial role in ensuring that miniature parts can be efficiently produced without defects. DFM is an engineering practice that optimizes part design, tooling, material selection and more. It starts with your initial design. From there, design engineers work with you to review your designs for moldability, dimensional stability, material compatibility and performance, and beyond. In this process, engineers can carefully evaluate whether the methods used for prototyping can be effectively scaled to full production while maintaining precision and efficiency.
The goal of DFM is to bridge the gap between design intent and actual production, helping manufacturers simplify and streamline the process right from the design phase.
Early collaboration with suppliers is a key to DFM success. Involving suppliers from the very beginning helps optimize material selection, tooling design and manufacturing processes. Suppliers bring invaluable insights that help reduce costs and lead times, while also identifying potential production hurdles. This collaborative approach leads to smoother, faster and more efficient product development.
“Micromolding is reshaping what’s possible in medical device design,” said Hoffer Plastics director of engineering, Brian Beringer. “We’re not just making smaller parts. We’re enabling smarter, more advanced solutions that improve lives. From ultra-precise diagnostic tools to next generation wearables and minimally invasive treatments, micromolding is driving a new era of medical innovation.”
2. Tooling & Mold Design
At the heart of successful micromolding is precision tooling. For medical devices, where components must meet stringent regulatory standards and perform reliably under demanding conditions, the importance of high-precision molds cannot be overstated. Leveraging the findings from the DFM and prototyping processes, manufacturers can move with confidence in their part and tooling designs. At this stage, companies can work with tooling partners to confidently scale tooling cavitation while ensuring all parts remain identical and within required tolerances. Through precision tooling expertise, process control and continuous quality monitoring, companies can make the successful transition from prototype tooling to full-scale production tooling.
3. Scalability: From Prototype to Production
Successfully scaling from early-stage prototyping to high-volume production in the medical device industry requires meticulous attention to consistency, quality and performance. Given the stringent demands for safety and reliability, manufacturers must maintain strict control throughout every phase of production, from initial design to finished device.
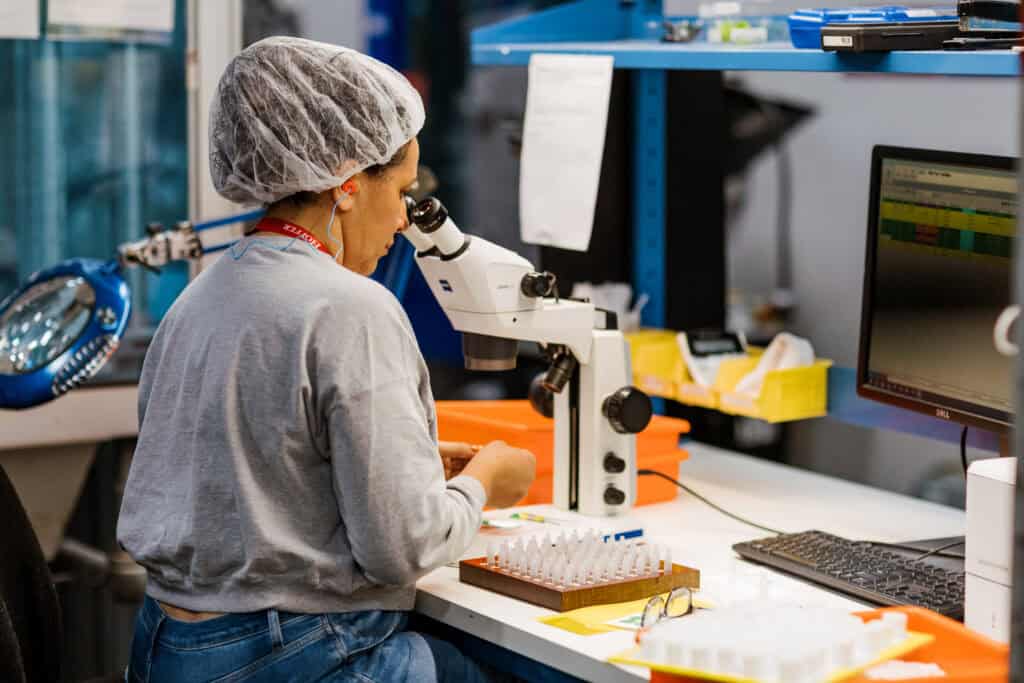
Micromolding plays a crucial role in this process by enabling a faster more efficient transition from design validation to full-scale production of highly precise, miniature components. Micromolding speeds this transition with confidence due to several key factors:
- Process Validation: With micromolded prototypes, you’re able to test your processes in the same production environment – even on the same equipment. This ensures fewer surprises when you scale.
- Material Selection: Micromolding allows you to prototype using final medical-grade resins like PEEK, LCP, nylons and beyond. This allows you to gain early insights into flow, shrinkage and overall material performance.
Not only does this approach meet growing demand for high-quality, reliable medical components, but it also allows companies to accelerate time-to-market, ensuring timely delivery of essential devices without compromising precision or safety.
Shaping the Future of Medical Devices Through Micromolding
By enabling the production of highly precise, miniaturized components, micromolding is driving innovation in the medical industry. From rapid prototyping to full-scale production, this technology is transforming the way medical devices are designed, manufactured and delivered, ultimately improving patient care and treatment outcomes.